Wind Power
Wind turbines are electrical devices that harness the power of the wind to generate electricity. They are composed of various components that work together to convert wind energy into mechanical work and then into usable electrical energy.
The history of wind energy dates back more than 3000 years, but it was in 1891 when Danish inventor Poul La Cour built the first windmill specifically designed to generate electricity. Later, in 1941-42, Danish engineer F.L. Smidth developed a windmill that can be considered as a precursor to the modern wind turbines we see today.
The principle behind wind power generation involves the conversion of wind energy into mechanical energy and then into electrical energy using specialized equipment. In essence, wind turbines can be regarded as engines that utilize the sun as the heat source and the atmosphere as the working medium.
They rely on the force of the wind to drive the rotation of their blades, which, in turn, prompts a generator to produce electricity through a speed-increasing mechanism.
A typical wind turbine is composed of a head, rotor, tail, and blades. However, wind turbines can be inherently unstable due to variations in wind strength. Consequently, the electricity output from a wind turbine fluctuates between 13 to 25 volts of variable AC power.
To ensure stable and consistent use, the generated electricity must be rectified by a charger and then stored in batteries, transforming the electrical energy into chemical energy.
Subsequently, an inverter power supply with a protection circuit is employed to convert the stored chemical energy back into AC 220V mains power, enabling a reliable power supply.
The core components of a wind turbine include:
Nacelle: This is the main housing that contains crucial equipment, such as the gearbox and generator. Maintenance personnel can access the nacelle through the wind turbine tower. The left end of the nacelle connects to the wind turbine rotor, comprising the rotor blade and shaft.
Rotor Blades: These blades are responsible for capturing the wind and transmitting its energy to the rotor shaft. In modern wind turbines, each rotor blade can measure approximately 20 meters in length, designed to resemble the shape of an airplane wing.
Rotor Shaft: The rotor shaft is connected to the low-speed shaft of the wind turbine, serving as the central component for transmitting the rotational energy.
Low-Speed Shaft: This shaft connects the rotor shaft to the gearbox. In modern wind turbines, the rotor speed is relatively slow, typically ranging from 19 to 30 revolutions per minute. The low-speed shaft contains conduits for the hydraulic system, which facilitates the operation of the aerodynamic gate.
Gearbox: Positioned on the left side of the nacelle, the gearbox increases the rotational speed of the high-speed shaft, achieving up to 50 times the speed of the low-speed shaft.
The high-speed shaft, along with its mechanical brake, operates at 1500 rpm and drives the generator. Additionally, the high-speed shaft is equipped with an emergency mechanical gate, which is utilized during aerodynamic gate failures or maintenance procedures.
Generator: Also known as an induction motor or asynchronous generator, this component is responsible for converting mechanical energy into electrical energy. Modern wind turbines typically feature generators with a maximum electrical output ranging from 500 to 1500 kW.
Yaw Device: This mechanism enables the nacelle to rotate, ensuring that the rotor continuously faces the direction of the wind. An electric motor controls the yaw device, which is operated by an electronic controller.
The controller detects wind direction through a wind vane and makes adjustments accordingly. Generally, the wind turbine only yaws a few degrees at a time in response to changes in wind direction.
You may like:
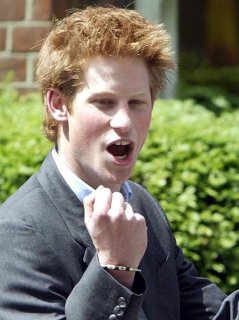
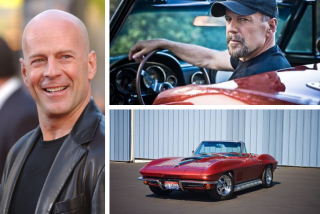
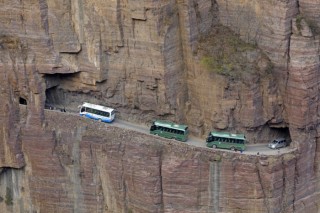
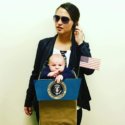